What is 3D printing?
3D printing is an additive manufacturing technology that creates physical objects by stacking and fusing layers of material. Unlike traditional manufacturing methods, which often involve removing material from a larger block or using molds, 3D printing builds parts layer by layer. This process allows for greater design flexibility and can produce complex geometries that are difficult or impossible to achieve with conventional techniques. It’s also a fast and cost-effective method with lower setup costs, making it ideal for prototyping and engineering applications, especially when creating lightweight or custom-designed components.
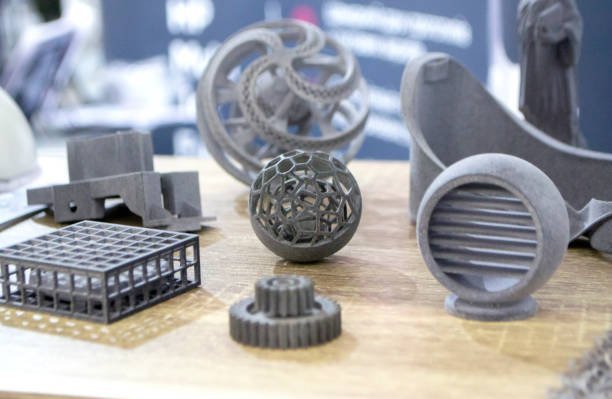
3D Printing and Additive Manufacturing
The term “3D printing” often conjures images of hobbyist projects, desktop printers, and low-cost materials like ABS and PLA. This association is due to the rise of accessible and affordable desktop 3D printers, especially those born out of the RepRap movement (a project aimed at creating self-replicating machines) in the late 2000s. Machines like the MakerBot and Ultimaker were instrumental in democratizing the technology, making it available to enthusiasts, students, and small-scale users. This movement reached a tipping point around 2009, when advancements in Fused Deposition Modeling (FDM), combined with these affordable machines, made 3D printing far more accessible to the general public.

On the other hand, additive manufacturing refers to the broader, industrial use of 3D printing technologies. In this context, it’s used for creating functional prototypes, specialized tools, and even production-ready parts in sectors such as aerospace, automotive, healthcare, and architecture. Additive manufacturing encompasses a wide variety of materials and processes, from polymers and metals to ceramics, and includes techniques like Selective Laser Sintering (SLS), Stereolithography (SLA), and Direct Metal Laser Sintering (DMLS). These processes are designed to handle high-end applications with superior precision and material properties.

In summary, while 3D printing is often linked with consumer-grade machines, additive manufacturing represents its more industrial counterpart, driving innovation across various fields with sophisticated techniques and materials.
3D Printing and Rapid Prototyping
The term “rapid prototyping” was initially used to describe 3D printing technologies when they first appeared in the 1980s. At that time, 3D printing was primarily limited to creating prototypes, as it lacked the capability to produce final, production-grade parts. These early technologies allowed for fast design iterations, enabling engineers and designers to quickly visualize and test concepts.
However, 3D printing has since evolved, and it’s now capable of producing high-quality, functional parts for end-use in industries such as automotive and aerospace. Today, rapid prototyping refers to any fast method of creating prototypes, not just 3D printing. Other technologies, like CNC machining, have also become widely used for this purpose, and as a result, rapid prototyping has become a more general term, encompassing all quick prototyping processes.

When Was 3D Printing Invented?
3D printing, often referred to as additive manufacturing, traces its roots back to the 1980s when it was initially developed to accelerate product development through faster prototyping.
- 1981: The first patent for a UV light-based method to cure photopolymers for rapid prototyping was awarded to Hideo Kodama in Japan. Despite his early contribution, the patent was abandoned due to a lack of commercial interest.
- 1984: French inventors Alain Le Mehaute, Olivier de Witte, and Jean Claude André also submitted a patent using UV light to cure photopolymers, but General Electric abandoned it, citing insufficient business potential.
- 1984: Just weeks later, Charles “Chuck” Hull in the U.S. filed his patent for an Apparatus for Production of Three-Dimensional Objects by Stereolithography (SLA), coining the term “stereolithography.” Hull is widely credited with inventing SLA and founded 3D Systems in 1987, launching the commercial SLA-1 machine.
Several other key technologies also emerged in the late 1980s:
- 1987: Carl Deckard invented Selective Laser Sintering (SLS) and co-founded DTM Corp.
- 1989: S. Scott Crump patented Fused Deposition Modeling (FDM) and founded Stratasys with his wife.
These early developments laid the foundation for what would become a rapidly evolving industry, with key milestones like the release of the SLA-1 in 1987, the first FDM printer by Stratasys in 1992, and the Sinterstation 2000 by DTM that same year, marking the start of 3D printing’s commercial applications.
Commercialization: During the late 1980s and early 1990s, 3D printing gained traction for industrial prototyping, particularly in automotive, aerospace, and healthcare sectors. Over the years, the technology matured and became more accessible.
Democratization: The early 2000s saw a rise in affordable 3D printers for hobbyists, led by projects like RepRap in 2005 and the launch of the MakerBot Cupcake CNC in 2009. Falling patents and growing material science developments further fueled this trend.
By the mid-2010s, 3D printing was no longer just for prototyping, but was being used for end-use production parts across industries. Today, the technology continues to expand into new areas, including bioprinting, construction, and consumer goods.

How Does 3D Printing Work?
Additive vs. Traditional Manufacturing
3D printing, also known as additive manufacturing, emerged in the 1980s as a new approach to production, contrasting sharply with traditional manufacturing methods that had been established long before. To illustrate the key differences, we can categorize manufacturing methods into three main groups: additive, subtractive, and formative manufacturing.
Additive Manufacturing
Additive manufacturing constructs 3D objects by layering and fusing 2D materials. This process requires minimal startup time and costs, making it particularly suitable for rapid prototyping. Parts can be created quickly and easily disposed of after use, and the ability to produce intricate geometries is one of 3D printing’s significant advantages.
However, a major limitation of additive manufacturing is that the resulting parts are often anisotropic (directionally dependent) and not fully dense, which can affect their material and mechanical properties compared to those created through subtractive or formative techniques. Additionally, variations in cooling or curing can lead to inconsistencies in different prints of the same part.
Subtractive Manufacturing
In contrast, subtractive manufacturing, which includes methods like milling and turning, involves removing material from a solid block (or “blank”) to create objects. This approach allows for great control over the manufacturing process, resulting in highly accurate parts with excellent repeatability. Subtractive methods often rely on Computer Aided Manufacturing (CAM) to optimize tool paths and material removal, though this adds setup time and costs.
The main drawback of subtractive manufacturing is that the cutting tools must access all surfaces, which limits design complexity. Even advanced 5-axis machines can struggle with intricate geometries, necessitating reorientation and adding to production time and costs. Furthermore, this method tends to be wasteful, as significant material is often removed to achieve the final shape.
Formative Manufacturing
Formative manufacturing encompasses techniques like injection molding and stamping, where materials are shaped through heat and/or pressure. These processes are designed to lower the marginal cost per part, but creating unique molds and machinery leads to high initial setup costs. Nevertheless, formative techniques can produce parts with remarkable consistency across a wide range of materials, making them the go-to choice for high-volume production runs.
Comparing Manufacturing Methods
Given the complexity of manufacturing, it’s challenging to compare each method comprehensively across multiple dimensions, including cost, speed, design complexity, material options, mechanical properties, surface finish, tolerances, and repeatability. However, some general guidelines can help:
- Additive manufacturing is ideal for low volumes, complex designs, and situations where speed is critical.
- Subtractive manufacturing excels in medium volumes, simple geometries, tight tolerances, and when working with hard materials.
- Formative manufacturing is most efficient for high-volume production of identical parts.
Ultimately, cost per part often dictates the most suitable manufacturing process. While each method has its strengths and weaknesses, understanding these can help industries make informed decisions about which manufacturing approach best suits their needs.
3D Printing Technology
With the diverse range of 3D printing technologies available today, understanding the various processes can be overwhelming. The International Organization for Standardization (ISO) established the ISO/ASTM 52900 standard to clarify the growing terminology associated with 3D printing.
Summary of the primary types of 3D printing
Below is a summary of the primary types of 3D printing processes:
- Vat Polymerization: In this process, liquid photopolymer resin is cured by a light source, typically UV light, to create solid objects layer by layer. Stereolithography (SLA) is a well-known method that falls under this category.
- Material Extrusion: This method involves the deposition of molten thermoplastic material through a heated nozzle. The most common example is Fused Deposition Modeling (FDM), which is widely used for both professional and hobbyist applications.
- Powder Bed Fusion: This technique fuses powdered materials using a high-energy source, such as a laser or electron beam. Selective Laser Sintering (SLS) and Electron Beam Melting (EBM) are examples of powder bed fusion technologies.
- Material Jetting: In this process, droplets of liquid photosensitive material are deposited onto a build platform and cured by light, allowing for the creation of detailed parts. PolyJet is a prominent technology within this category.
- Binder Jetting: Here, a binding agent is deposited onto a bed of granulated materials, typically metal or sand, and later sintered together to form a solid part. This method is often used for creating complex geometries in metal printing.
- Direct Energy Deposition: In this technique, molten metal is deposited and simultaneously fused to build up parts, making it suitable for repairs and adding material to existing components.
- Sheet Lamination: This process involves cutting individual sheets of material to shape and then laminating them together. Paper Lamination and Metal Laminating are examples of this method.
These various 3D printing technologies cater to different applications and materials, allowing industries to select the most appropriate method based on their specific needs. For more detailed information, you can refer to the full overview on 3D printing technologies here.
3D Printing Processes
There are seven primary 3D printing processes, each encompassing unique technologies and various brands offering similar printers. Here’s an overview of each process:
1. Vat Photopolymerization
In vat photopolymerization, a photopolymer resin is cured by exposure to specific wavelengths of light. The main technologies under this category include Stereolithography (SLA), Direct Light Processing (DLP), and Continuous Direct Light Processing (CDLP).
- SLA uses a UV laser beam to selectively cure resin layer by layer.
- DLP utilizes a digital light projector to flash an entire layer at once.
- CDLP relies on the continuous upward motion of the build plate for curing.
Benefits:
- Smooth surfaces and fine details
- Excellent for rapid prototyping, especially in jewelry and medical applications
Limitations:
- Parts tend to be brittle
- Often require support structures
- Sensitive to UV light
- Extensive post-processing is needed
2. Powder Bed Fusion
Powder Bed Fusion (PBF) technologies utilize a heat source to fuse plastic or metal powder particles layer by layer. Techniques like Selective Laser Sintering (SLS), Electron Beam Melting (EBM), and Multi Jet Fusion (MJF) are examples of this process.
Benefits:
- Produces strong parts, especially in nylon
- Capable of complex geometries
- Scalable to different sizes
- No need for support structures
Limitations:
- Longer production times
- Higher costs for machines, materials, and operation
3. Material Extrusion
Material extrusion involves squeezing a material through a nozzle onto a build plate layer by layer. Fused Deposition Modeling (FDM) is the most prevalent technology in this category.
Benefits:
- Fast and low-cost
- Compatible with common thermoplastics
Limitations:
- Rough surface finish
- Anisotropic properties (strength varies with direction)
- Usually requires supports
- Limited accuracy and scalability
4. Material Jetting
Material jetting uses UV light or heat to harden photopolymers, metals, or wax to build parts layer by layer. Nano Particle Jetting (NPJ) and Drop-on-Demand (DOD) are two types of material jetting.
Benefits:
- Creates realistic prototypes with excellent details
- High accuracy and smooth surface finish
Limitations:
- Higher cost
- Often has brittle mechanical properties
5. Binder Jetting
Binder jetting employs an industrial printhead to apply a binding agent onto layers of powder material, which do not require heat to bind.
Benefits:
- Offers full-color options
- Wide range of materials
- No support structures needed
- Minimizes warping or shrinking
Limitations:
- Lower part strength
- Less accurate compared to material jetting
6. Direct Energy Deposition
Direct Energy Deposition (DED) melts powder material as it is deposited, primarily using metal powders or wire. Techniques like Laser Engineered Net Shape (LENS) and Electron Beam Additive Manufacturing (EBAM) are part of this category.
Benefits:
- Strong parts with a variety of materials
- Capability to produce larger parts
Limitations:
- High costs
- Poor surface finish
7. Sheet Lamination
Sheet lamination involves stacking and laminating thin sheets of material using methods like bonding, ultrasonic welding, or brazing.
Benefits:
- Fast and low-cost
- Does not require support structures
- Capable of multi-material layers
Limitations:
- Requires post-processing
- Limited materials available
- Variability in finishing quality
Selecting the Right 3D Printing Processes
Choosing the appropriate 3D printing process for a specific part can be challenging, as multiple options may be viable, each yielding different costs and outputs. To make an informed decision, consider the following three key aspects:
- Material Properties: Assess the required attributes of the material, including strength, hardness, and impact resistance. Different printing processes offer varying capabilities regarding these properties.
- Design Requirements: Evaluate both functional and visual design needs, such as the desired surface smoothness, structural integrity, and resistance to heat. The chosen process should align with these design goals.
- Process Capabilities: Consider the specifications of the 3D printing method, including its accuracy and maximum build size. Each process has unique strengths and limitations that can affect the final product.
To effectively select the right 3D printing process, you can categorize your decision-making based on:
- Material Requirements: Identify the material that best meets your part’s needs.
- Functional or Visual Characteristics: Determine the primary functionalities and aesthetics your part must achieve.
- Accuracy or Build Size: Consider the dimensional accuracy required and the size constraints of your design.
By evaluating these factors, you can streamline your selection process and ensure that you choose the most suitable 3D printing method for your specific application.
For more detailed information, you can refer to various resources on 3D printing processes and selection criteria, such as the article from ProtoTi
3D Printing Materials: A Comprehensive Overview
The landscape of 3D printing materials is continually evolving, driven by increasing market demands for specific material properties and innovations in material science. Although it’s challenging to provide a complete overview due to the sheer variety of available materials, we can categorize them based on compatibility with different 3D printing processes.
Common Types of 3D Printing Materials
- Thermoplastic Polymers: These are the most widely used materials in 3D printing. They can be melted and reshaped multiple times. Common examples include:
- PLA (Polylactic Acid): Popular among hobbyists for its ease of use and biodegradability.
- ABS (Acrylonitrile Butadiene Styrene): Known for its toughness and impact resistance, often used in functional prototypes.
- Thermoset Polymers: Unlike thermoplastics, thermosets undergo a curing process that makes them hard and rigid. They are typically used in applications requiring high strength and heat resistance.
- Metals: Various metals can be 3D printed, especially in industrial applications. Common metal materials include:
- Stainless Steel
- Titanium
- Aluminum
These materials are often used for aerospace, automotive, and medical applications due to their excellent mechanical properties.
- Composites: These materials combine polymers with other substances, such as carbon fiber or glass fiber, to enhance strength and durability while reducing weight.
- Ceramics: Used for high-temperature applications, ceramics are typically used in specific sectors such as dentistry and engineering.
Material Properties
Materials can also be classified based on their properties, including:
- Cost: Options range from low-cost materials suitable for hobbyists to high-performance materials for industrial applications.
- Chemical Resistance: Some materials are designed to withstand harsh chemicals.
- Flexibility and Durability: Materials like Nylon 12 are favored in industrial settings for their durability.
- Heat and Water Resistance: Essential for applications that require resilience to extreme conditions.
As technology progresses, new materials continue to emerge, expanding the possibilities for various applications in both industrial and consumer sectors.
For further insights and details on specific materials and their applications, you can explore comprehensive resources like those provided by ProtoTi.
Post-Processing 3D Prints: Enhancing Finish and Performance
Post-processing is essential for improving the aesthetics and mechanical properties of 3D-printed parts. The choice of technique largely depends on the desired finish and functionality of the part.
Common Post-Processing Techniques
- Polishing: For resin prints, polishing can achieve a glossy or reflective finish, enhancing the visual appeal.
- Vapor Smoothing: This method involves exposing the print to chemical vapors, causing the surface layer to melt and create a smooth, glossy finish. It’s effective for certain materials that can withstand this treatment.
- Sanding: Sanding helps remove visible layer lines and rough textures, allowing for a smoother surface. This technique is often used as a precursor to painting.
- Priming and Painting: If color or specific aesthetics are important, priming and painting are common practices. This is useful for both visual appeal and safety, particularly in applications where visibility is key.
- Heat Treatment: This technique can enhance the mechanical properties of a part, making it stronger or more heat resistant.
- Electroplating: This method adds a metal layer to the surface, improving durability and aesthetics. However, its feasibility depends on the original material, so it’s crucial to consult with your manufacturing provider.
- Inserts and Threading: For functional applications, adding metal inserts can reinforce parts, while threading allows for easier assembly with screws or bolts.
By utilizing these post-processing techniques, you can significantly enhance the performance and appearance of your 3D-printed parts, tailoring them to specific applications and aesthetic requirements.
For a more detailed overview of each post-processing technique, you can check out resources like Prototi’s guide on 3D printing.
3D Printing Software: Essential Tools for Design and Production
The 3D printing process begins with software, and there are various programs designed to assist in each phase, from 3D modeling to print simulations and slicing. Selecting the right software is crucial for achieving the desired outcomes in your projects.
Key Software Categories for 3D Printing
- 3D Modeling Software:
- Solid Modeling: This approach involves creating virtual objects by defining and joining 3D shapes, usually starting with predefined forms. Solid modeling is generally more efficient for simple, non-organic shapes. Popular software in this category includes:
- SolidWorks
- Fusion 360
- Rhinoceros 3D (Rhino)
- Surface Modeling: In contrast, surface modeling begins with 2D shapes, allowing designers to manipulate them into freeform 3D shapes. This method is often favored for organic and complex designs. Both solid and surface modeling can yield similar outputs, but each excels in different contexts depending on the complexity and nature of the design.
- Slicing Software: Once a 3D model is created, it needs to be sliced into layers for printing. This is where slicing software comes into play. It converts the 3D model into G-code, which the printer understands. Popular slicing programs include:
- Ultimaker Cura
- PrusaSlicer
- Simplify3D
- Print Simulation Tools: These tools help visualize the printing process and can identify potential issues before actual printing begins. They can be essential for optimizing print settings and ensuring the best possible results.
- File Error Fixers: Often, 3D models can contain errors that prevent successful printing. Software tools designed to repair these files can save time and frustration. Programs like Meshmixer and Netfabb are widely used for this purpose.
With a variety of software available, choosing the right tools can streamline your 3D printing workflow, whether you’re a professional or a hobbyist. For a comprehensive overview of 3D printing software options, check out more resources from sites like Prototi and other dedicated 3D printing platforms.