In a study published on ScienceAdvances, US researchers from Stanford Nano Shared Facilities (SNSF) and Lawrence Livermore National Laboratory (LLNL), with support from the National Science Foundation and the US Department of Energy, have demonstrated the high absorptivity benefits of nanotextured powders in LPBF of challenging metals such as copper, silver and tungsten.
Metal additive manufacturing (AM) is a revolutionary process, but printing metals like copper, silver, and tungsten is challenging due to their high reflectivity. These metals do not absorb enough laser energy during Laser Powder Bed Fusion (LPBF), leading to inefficient energy use, poor part quality, and high power requirements. However, a new process using nanotextured metal powders can overcome these challenges by significantly enhancing powder absorptivity and improving the efficiency of additive manufacturing.

Metals like copper and silver reflect a large portion of laser energy, which reduces heat localization needed for proper fusion. Refractory metals, such as tungsten, have high melting points and thermal conductivities, leading to cracking during cooling. Attempts to print these metals often involve increasing laser power or adding alloying elements. However, these methods are costly, reduce material properties, and can damage printing equipment.
What are nanotextured powders?
Nanotextured powders are metal powders modified with nanoscale grooves on their surface. These grooves, created using chemical etching, increase the surface area and enhance the interaction between the laser and the powder. This leads to significantly higher laser energy absorption without altering the material’s chemical composition.
The etching process involves submerging metal powders in a solution that creates nanoscale features on their surface. For example, copper powders were etched using a ferric chloride (FeCl₃) solution, which produced powders with different levels of surface roughness based on the etching time.
The enhanced absorptivity of the nanotextured powders results from two main factors. One is Plasmonic Resonance: the nanoscale grooves concentrate light energy, resulting in localized heating and higher absorption. The other is Multiple Scattering Events: here the textured surface causes multiple reflections of laser energy, increasing overall absorption.
Benefits of nanotextured powders in AM
Nanotextured powders enable the printing of metals like copper and tungsten at significantly lower energy densities. For example, pure copper was printed at a 92% relative density using just 83 J/mm³ of energy, which is much lower than traditional methods.
At lower laser powers, the enhanced absorptivity of nanotextured powders leads to improved part quality with fewer defects. This process also minimizes the need for post-processing, making it more cost-effective.
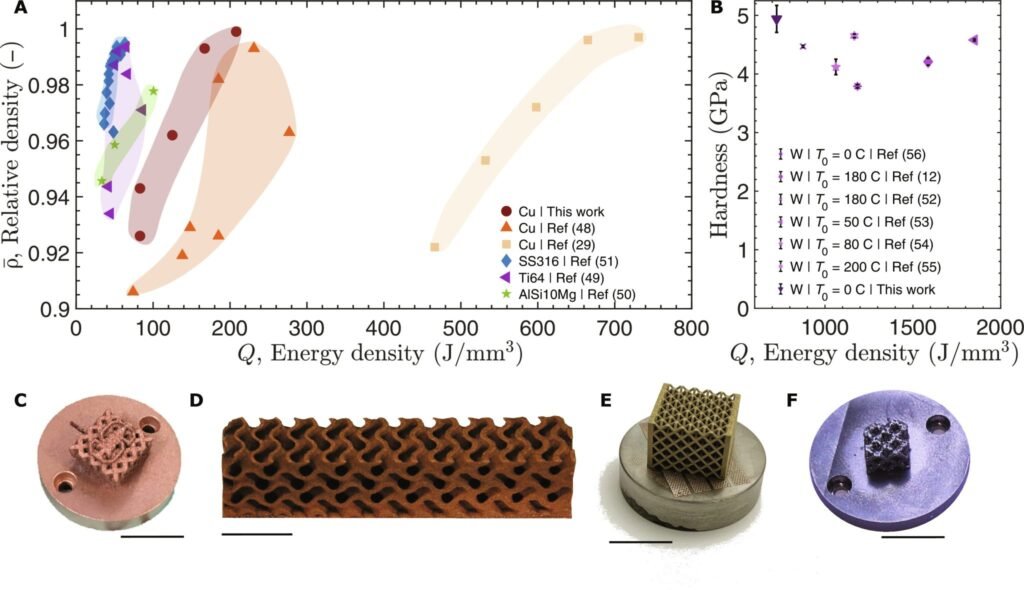
This method has been successfully applied to copper, silver-copper alloys, and tungsten, demonstrating its versatility for a wide range of high-reflectivity and refractory metals.
With nanotextured copper powders, the researchers achieved high-density parts at energy levels significantly lower than traditional methods. At 100 W and 300 mm/s, a relative density of 92.6% was reached, compared to 85.6% for non-textured powders. For tungsten, the nanotextured powders enabled successful printing at lower laser powers, resulting in high-density parts and improved mechanical properties. This marks a breakthrough in printing refractory metals.
