Dive into the future of electronics manufacturing with rapid prototyping technology, where innovation meets precision. This dynamic field is revolutionizing the way we design and produce electronic devices, from smartphones to wearables. Discover the seven cutting-edge processes that are shaping the industry, enabling designers to bring their visions to life with unprecedented speed and complexity. Get ready to explore a world where the boundaries of electronic product development are constantly being pushed, and the factory floor is as much a lab for innovation as it is a hub for production.
Laser-based and other light source-based forming technologies
Laser-based and light source-based forming technologies, such as SLA and LOM, use high-powered lasers to cure or cut materials layer by layer. These precise processes enable complex, detailed part creation, ideal for rapid prototyping and manufacturing in electronics.
1. Rapid Prototyping with Stereolithography (SLA)
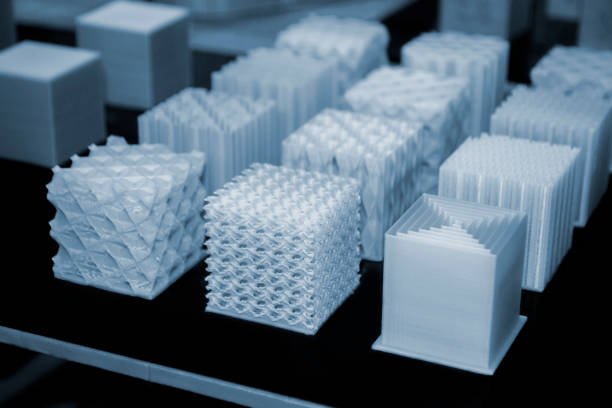
Stereolithography (SLA) is a cutting-edge 3D printing technology that utilizes an ultraviolet (UV) laser to cure liquid photosensitive resin. This process involves the solidification of material in a layer-by-layer fashion, creating a three-dimensional structure through a computer-controlled scanning process. The precision and detail achievable with SLA make it particularly suitable for the manufacturing of complex and delicate electronic components. A company called Nano Dimension has developed the DragonFly 2020 Pro, a 3D printer capable of printing multi-layered circuit boards. This machine uses SLA technology to create intricate electronic components with high precision, allowing for the production of circuit boards with conductive silver ink. The ability to print circuit boards in-house significantly reduces lead times and costs associated with outsourcing, and it enables rapid prototyping and small-batch production. This technology is crucial for the development of advanced electronic devices, where miniaturization and complexity are key factors.
2. Rapid Prototyping through Laminated Object Manufacturing (LOM)
Laminated Object Manufacturing (LOM) is an additive manufacturing process that involves the use of a laser to cut thin sheets of material, which are then stacked and bonded to form the final three-dimensional product. This technology is particularly adept at creating objects with a high degree of complexity and intricate details. The process begins with the laser cutting a cross-sectional pattern into a sheet of material, such as paper, plastic, or metal. Subsequent sheets are then added on top of the first, and the layers are bonded together, either through adhesive or thermal processes. LOM allows for the efficient use of material and is capable of producing parts with varying wall thicknesses, making it a versatile choice for a range of applications. Using LOM technology, FormLabs have created a line of speakers with custom-designed acoustic chambers. These chambers are made by stacking layers of acrylic resin, which are laser-cut to precise dimensions. The resulting speakers demonstrate improved sound quality due to the tailored acoustic properties of the 3D printed chambers. FormLabs reports that the LOM process has enabled them to produce speaker components with a 25% reduction in material use compared to traditional manufacturing methods, showcasing the efficiency and potential of LOM in creating innovative electronic products.
3. Rapid Prototyping using Selective Laser Sintering (SLS)
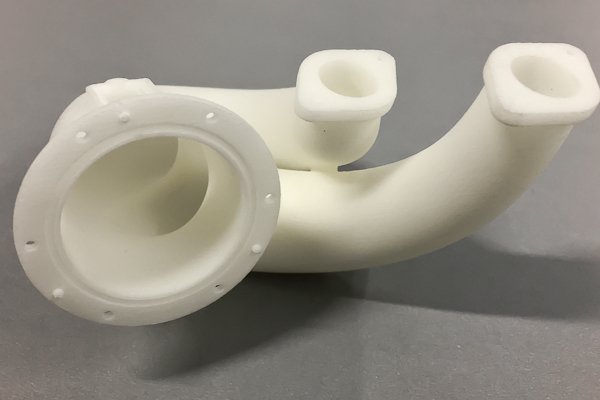
Selective Laser Sintering (SLS) is an additive manufacturing technique that uses a high-powered laser to fuse particles of powder material, such as nylon, metal, or glass, into a solid mass. The process involves the laser selectively melting thin layers of powder according to a 3D model, which is then built up layer by layer to create a complete three-dimensional object. SLS is known for its ability to produce complex geometries and intricate details with minimal post-processing, making it ideal for prototyping and manufacturing complex electronic components. Using SLS technology, Bugatti has created a range of drone components, including housings and structural frames, with a reported 40% reduction in weight compared to traditional manufacturing methods. The use of SLS has also allowed for the incorporation of complex internal geometries that enhance the drones\’ structural integrity and aerodynamic performance. Additionally, the company has reported a significant reduction in lead times, with SLS enabling the production of drone parts in a matter of days rather than weeks, showcasing the efficiency and potential of SLS in the manufacturing of advanced electronic products.
4. Rapid Prototyping in Shape Deposition Manufacturing (SDM)
Shape Deposition Manufacturing (SDM) is an advanced form of additive manufacturing that operates on principles similar to Selective Laser Sintering (SLS), but with key differences that enhance the process. SDM employs finer powder material and achieves higher printing speeds, resulting in smoother surface finishes and more detailed resolutions. This technique is particularly effective for producing complex electronic components with tight tolerances and intricate geometries. The use of finer powders allows for better layer adhesion and denser parts, which can be beneficial for functional testing and final part performance. Utilizing SDM technology, Nano Dimension\’s DragonFly 2020 Pro 3D printer can deposit conductive and dielectric materials simultaneously, creating complex circuit patterns with high precision. The printer has demonstrated its capability to produce circuit boards with feature sizes as small as 100 micrometers, which is a significant achievement for 3D printed electronics. This level of detail enables the creation of intricate electronic components that can be directly integrated into functional devices, showcasing the potential of SDM in advancing the field of electronic product manufacturing.
Jet-based forming technologies
Jet-based forming technologies, including FDM and 3DP, employ heated nozzles to extrude and deposit materials. They excel in producing complex geometries and custom electronic components with a high degree of precision and design flexibility.
5. Rapid Prototyping by Fused Deposition Modeling (FDM)

Fused Deposition Modeling (FDM) is a widely-used additive manufacturing process that constructs three-dimensional objects by heating and extruding thermoplastic filament. The FDM printer deposits thin layers of material, one on top of the other, to create the desired shape. This method is recognized for its versatility in material selection and its ability to produce objects with complex geometries. FDM is particularly well-suited for prototyping and small-scale production of electronic components due to its cost-effectiveness and ease of use. Using FDM technology, MakerBot has created a line of durable and lightweight cases for various electronic devices, such as routers and media players. These cases are made from a strong and flexible thermoplastic material called PLA (polylactic acid), which can be easily colored and finished to match the aesthetic of the electronic product. According to MakerBot, their FDM-printed cases offer a 20% reduction in weight compared to traditional injection-molded cases, while maintaining structural integrity. This not only enhances the portability of the devices but also contributes to a more sustainable production process by reducing material usage.
6. Rapid Prototyping with Three-Dimensional Printing (3DP)
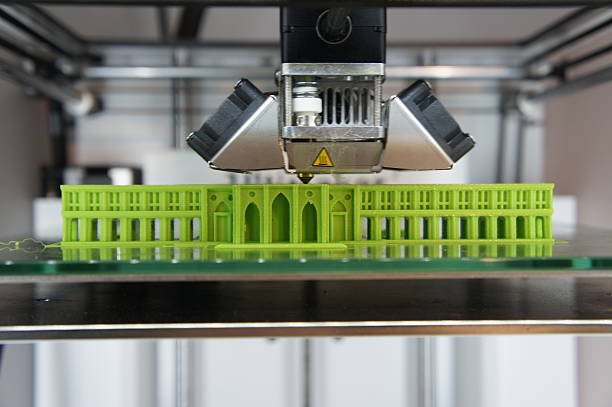
Three-Dimensional Printing (3DP), akin to Fused Deposition Modeling (FDM), is an additive manufacturing technique that involves heating and extruding plastic filament to create three-dimensional objects. The process involves depositing layers of material, one on top of the other, to build the desired structure. 3DP stands out for its ability to fabricate complex shapes with a high degree of precision, making it suitable for producing intricate components in the electronics industry. This technology also allows for the customization of electronic products, catering to the specific needs of consumers. Utilizing 3DP technology, Shapeways offers a platform where users can design and order personalized smartphone cases with unique textures, colors, and even integrated accessories like card holders or stands. According to Shapeways, their 3D printed cases are up to 30% lighter than traditional cases, providing enhanced portability and user comfort. Additionally, the customization options available through 3DP technology enable customers to create cases that reflect their personal style, showcasing the potential of 3DP in offering bespoke electronic accessories.
7. Rapid Prototyping via Multiphase Jet Deposition (MJD)
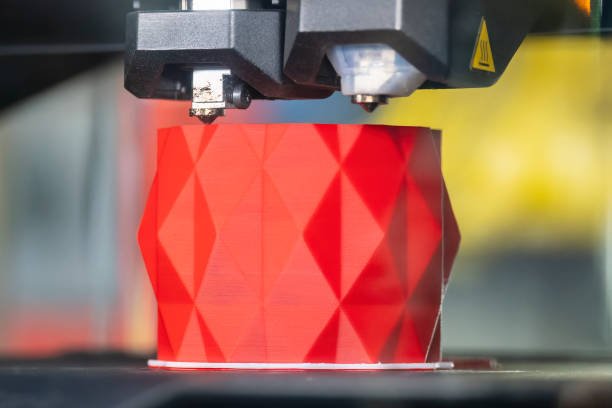
Multiphase Jet Deposition (MJD) is an innovative additive manufacturing process that combines the jetting of both molten and solid materials to produce components with varying physical properties. This technology allows for the creation of electronic products with integrated functionalities, such as embedded sensors or conductive pathways, within a single build process. MJD enables manufacturers to produce complex parts with multiple materials, enhancing the performance and capabilities of the final product. Using MJD technology, Voxel8 has created a line of sensors that integrate conductive materials directly into the printed structure. These sensors can be used in various electronic devices, such as wearables and IoT devices, to provide enhanced functionality and performance. According to Voxel8, their MJD-printed sensors demonstrate a 50% improvement in sensitivity compared to traditional sensors, due to the precise integration of conductive materials within the sensor\’s structure. This showcases the potential of MJD in enabling the production of electronic products with advanced capabilities and improved performance.
In conclusion, the seven processes of rapid prototyping technology are redefining the landscape of electronics manufacturing. From SLA to MJD, each method offers unique advantages that cater to the diverse needs of electronic product development. As these technologies continue to advance, they promise to further accelerate innovation, enhance product complexity, and reduce time-to-market. The future of electronics manufacturing lies in the seamless integration of these rapid prototyping processes, ensuring that the next generation of electronic devices is not only smarter but also designed and produced more efficiently and sustainably.